The Fleet Operator Recognition Scheme (FORS) is a voluntary accreditation scheme for fleet operators which aims to raise the level of quality within fleet operations and to demonstrate which operators are achieving exemplary levels of best practice in safety, efficiency, and environmental protection.
Becoming a FORS member can bring you the peace of mind that your company is managing its work-related road risk (WRRR) – and demonstrates to your customers and supply chain your commitment to exceeding the industry standard.
FORS encourages operators to take a closer look at their operation and identify areas of strength to be exploited and areas for improvement to be addressed. A successful Bronze audit reassures an operator that their operation is being run safely, efficiently and in an environmentally sound manner. The FORS logo allows potential customers to readily distinguish FORS operators from other operators.
Who requires the FORS Accreditation?
Although the FORS scheme is voluntary, many large-scale infrastructure projects require suppliers and partners to obtain accreditation before being included within the supply chain. As a result, FORS continues to enhance standards and quality levels.
Many sectors recognise the FORS accreditation scheme as a mark of distinction, including construction, fleet operations, waste management, rail, infrastructure, wholesale and retail.
What are the Fleet Operator Recognition Scheme requirements?
The FORS scheme takes into account various aspects of fleet transport including environmental factors (fuel efficiency and emissions), safety considerations and general operations. This combination of elements sets the standard for businesses within the plant, transport and fleet sectors and provides a benchmark for these businesses to aspire to.
Companies are assessed via specially designed audits which include risk assessments and reviews of policies and procedures. This demonstrates compliance against certain benchmarks, providing an overall score that translates into FORS Bronze, FORS Silver or FORS Gold status. Those who achieve FORS Gold status demonstrate the highest standards of compliance.
To achieve the higher grades of Silver and Gold, a company has to maintain and improve its Bronze accreditation. Additionally, to achieve Silver and Gold, attendance at a professional training course is required for Managers and Drivers.
The FORS Daily Walkaround Checks
The FORS Standard defines requirements that must be met by fleet operators if they
wish to become FORS Bronze, Silver or Gold accredited.
The walkaround check procedure shall include an inspection of the whole vehicle, trailer and any specialist equipment. In particular, the walkaround check shall cover the serviceability of:
- Wheels and tyres
- Brakes and steering
- Lights and markers
- Mirrors and window glass
- Obstructions to driver vision
- Bodywork condition
- Fluid levels and any leakages
- Vehicle safety equipment
In addition to the checks above, the following items need to be fitted/ installed and checked during the daily walkaround check as per accreditation.
FORS Bronze accreditation
Confirms that you employ good practice and comply with the requirements laid out by the FORS Standard. This includes demonstrating dedication to driver and vehicle safety, combined with improving operating practices through effective monitoring of fuel and tyre usage.
The following items need to be installed and checked as part of the daily walkaround check:
- A camera system that monitors the near-side vehicle blind spot.
- An in-cab display screen to provide the driver with a view of the near-side blind spot
- An in-cab audible warning system to alert the driver of other road users in the near-side blind spot
FORS Silver accreditation
Confirms that you employ good practice and comply with the requirements laid out by the FORS Standard. By achieving FORS Silver accreditation your fleet will be compliant with the CLOCS Standard for Construction Logistics and with TfL’s WRRR (Work Related Road Risk).
The following items need to be installed and checked as part of the daily walkaround check:
- Close-proximity sensors and blind-spot camera
- Audible warning system for vehicle turning left
- Audible warning system for vehicle reversing
- Rearview camera for vehicles over 7.5 tonnes gross weight
FORS Gold accreditation
Requirements primarily involve best practice measures, including you promoting the FORS Standard through your supply chain and demonstrating meaningful improvements against the baseline data gathered in FORS Silver.
The following items need to be installed and checked as part of the daily walkaround check:
Where a tolerance has been accepted at Silver requirement S6 to allow for older vehicles in the fleet replacement cycle, all HGVs at Gold requirement G6 (irrespective of age) shall be fitted with:
- A camera system that monitors the near-side vehicle blind spot
- An in-cab display screen to provide the driver with a view of the near-side blind spot
Vehocheck and FORS
Vehocheck compliance and fleet management software can provide fleets with a big helping hand in their efforts to secure and maintain FORS accreditation.
Vehocheck can drastically simplify the processes associated with defect reporting and fleet management, providing fleet managers with high levels of insight into the performance of both vehicles and drivers as well as defect and fleet management. Vehocheck can facilitate dynamic, real-time vehicle and driver compliance and track the progress of vehicles maintenance as well as provide an in-depth picture of how vehicles and drivers perform.
The Vehocheck vehicle compliance app enables drivers to perform FORS Daily Walkaround checks with ease, with a library of FORS vehicle checks available for each accreditation, all of which can be tailored to suit your fleet and business.
About Vehocheck
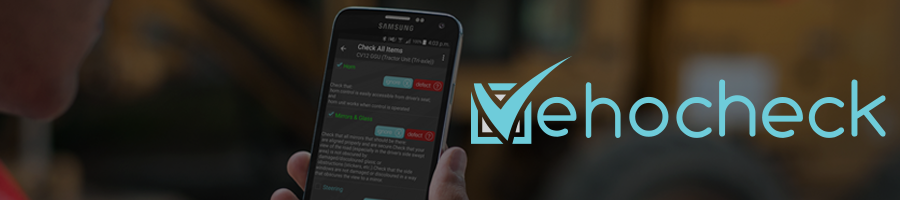
Vehocheck is a fleet management and compliance software solution for operators, drivers and workshops, which provides a fully traceable vehicle maintenance, compliance and repair audit for all your assets or vehicles.
The process from vehicle defect identification and managing the repair is enhanced through our workshop job card system, customised reporting to highlight driver behaviour and vehicle issues, with additional in-depth repair cost analysis.
By instantly delivering crucial asset or vehicle defect information, the procedures for correcting these issues can be expedited; enabling companies to maintain a productive, safe and compliant fleet.